Have you ever wondered about the journey your cotton bedsheet has taken to reach you? It’s a story that begins in a field with a tiny seed and ends in the comfort of your home. In this blog post, we’re going to unravel this fascinating journey. We’ll explore the life of a cotton plant, the art and science of turning fluffy cotton bolls into strong, fine yarn, and the process of weaving that yarn into the soft, durable fabric we know and love. So, let’s embark on this journey together, from seed to sleep, and discover the incredible process of making a cotton bedsheet.
Step 1: The Life of a Cotton Plant
Cotton, a plant that thrives in tropical and subtropical regions, begins its journey as a tiny seed. There are four main types of cotton, with upland cotton being the most widely produced.
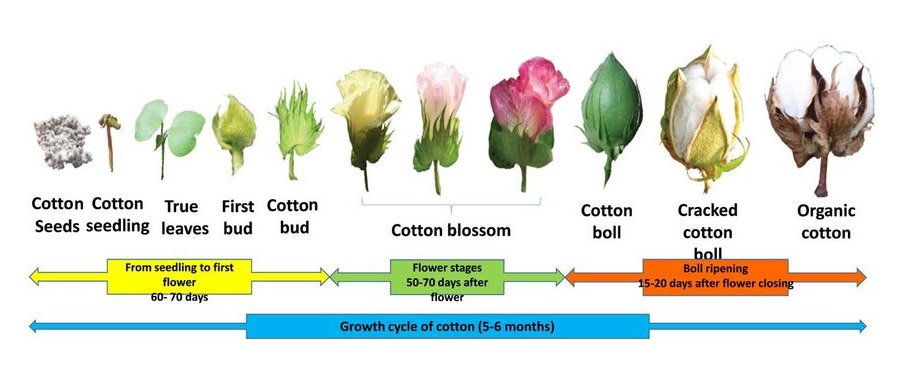
Once planted in the spring, the cotton seed germinates and grows into a plant with a strong stem and broad leaves. After about two months, the plant flowers. These flowers eventually fall off, leaving behind a small pod known as a cotton boll.
Inside the boll, cotton fibers develop around the seeds. After another two months, the bolls ripen and burst open, revealing the fluffy, white cotton.
Harvesting comes next, a process that requires perfect timing to ensure the cotton is picked when the bolls are fully open but before the weather can damage the fibers. Whether handpicked or harvested by machines, this marks the end of the first stage in the journey of a cotton bedsheet. The raw cotton must now be processed and transformed into a form that can be woven into a bedsheet.
Step 2: From Cotton Balls to Fibers
Once the cotton is harvested, it’s time to transform the fluffy balls into raw cotton fibers. This process begins with the separation of the cotton fibers from the seeds, a task accomplished by a machine known as a cotton gin.
Cotton ginning is a critical step in the journey of a cotton bedsheet. Invented by Eli Whitney in the late 18th century, the cotton gin revolutionized the cotton industry. The machine works by pulling the cotton through a series of small wire hooks that separate the seeds from the fibers.
After ginning, what’s left is raw cotton lint and cotton seeds. The seeds can be used for cottonseed oil or as a supplement in livestock feed, ensuring no part of the cotton plant goes to waste.
The raw cotton lint still contains some impurities, such as dirt and plant material, which need to be removed. This is done in the cleaning process, where the cotton is beaten with large brushes to remove the debris.
The cleaned cotton then goes through a process called carding. During carding, the cotton fibers are disentangled, straightened, and aligned into a thin, soft strand known as a sliver. Carding also removes any remaining impurities and short fibers, ensuring that only the longest and strongest fibers are left. These are the fibers that will be spun into the yarn for your cotton bedsheet.
At the end of this stage, the cotton has been transformed from fluffy bolls into clean, carded slivers ready for spinning. The journey from seed to sleep continues, bringing us one step closer to the finished bedsheet.
Step 3: Spinning Cotton Fibers into Yarn
The transformation of cotton fibers into yarn, a process known as spinning, is a critical step in the creation of a cotton bedsheet. This process involves twisting the cotton fibers together to form a thread or yarn. While spinning was traditionally done by hand, today it’s typically performed using high-speed, automated spinning machines.
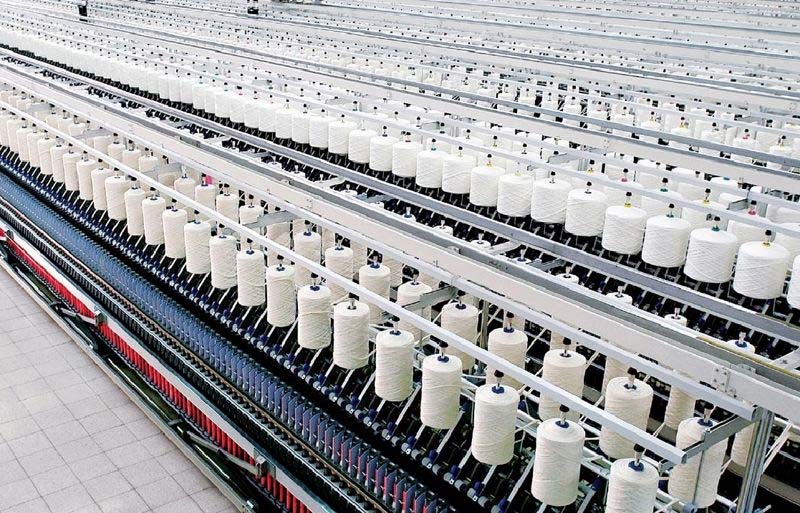
In the modern spinning process, cotton slivers from the carding stage are drawn out and twisted into a thin, strong thread known as roving. This roving is then further drawn out and twisted to create the final yarn. The amount of twist in the yarn determines its strength, thickness, and feel.
Throughout this process, stringent quality control measures are in place to ensure the yarn is strong, uniform, and free from defects. The end result is a strong, fine yarn, wound onto bobbins or cones, ready for the next stage: weaving. The journey from cotton seed to bedsheet continues, with each twist bringing us closer to the final product.
Step 4: Weaving Yarn into Fabric
With the yarn spun and ready, the next stage in the journey of a cotton bedsheet is the transformation of yarn into fabric through a process known as weaving. Weaving involves interlacing two sets of yarn – the warp and the weft – at right angles to each other to create a fabric.
In the weaving process, the warp threads are held taut and in parallel on a frame or a loom while the weft thread is woven over and under the warp threads. The warp threads give the fabric its length and strength, while the weft threads give it its width.
There are different types of weave that can be used in the production of cotton bedsheets, each with its own characteristics. For example, percale is a type of weave that is closely woven and produces a smooth and durable fabric. Sateen, on the other hand, has a weave that places most of the threads on the surface, creating a fabric with a silky feel and a glossy sheen.
The type of weave used can greatly impact the final product, affecting everything from the feel and appearance of the fabric to its durability and breathability. After the weaving process, the fabric is inspected for any defects, and then it’s off to the finishing process, where it will be prepared for its final transformation into a bedsheet.
Part 5: Finishing the Fabric
Once the cotton yarn has been woven into fabric, it’s time for the finishing touches that will transform it into a bedsheet. The finishing process involves several steps, each designed to enhance the fabric’s appearance, feel, and durability.
First, the fabric may undergo bleaching to remove any remaining impurities and to prepare it for dyeing. Bleaching turns the fabric a bright, clean white, providing the perfect canvas for any colors or patterns that will be added later.
Next comes the dyeing process, where the fabric is immersed in a bath of dye to give it color. The fabric can be dyed a solid color, or different colors can be used to create patterns or prints. In some cases, the fabric may be printed after dyeing, using specialized inks and printing techniques to add detailed designs.
Once the fabric has been dyed and printed, it’s time for the cutting and sewing process. The fabric is cut into the required shapes and sizes for different types of bedsheets, such as single, double, queen, or king. The edges are then hemmed to prevent fraying, and any additional features, like elastic corners or decorative details, are added.
The finished product is a soft, colorful, and durable cotton bedsheet, ready to be packaged and sent off to stores. From a tiny cotton seed to a beautiful bedsheet, the journey is a testament to the marvel of textile production.
Step 6: Quality Control and Packaging
Before the finished bedsheets can be sent to stores, they must undergo rigorous quality control measures. This ensures that every product meets the high standards expected by consumers. Inspectors check the sheets for any defects, such as incorrect sizing, loose threads, or color inconsistencies. Only those that pass these checks are approved for sale.
Once approved, the bedsheets are prepared for packaging. They are neatly folded, often along with care instructions and any branding materials. The packaged bedsheets are then boxed and prepared for shipment.
The journey from the factory to the store can be a long one, involving multiple modes of transport and possibly crossing international borders. But once they reach the store, these cotton bedsheets are ready to be purchased, taken home, and used to provide comfort and style in bedrooms around the world.
Step 7: The Environmental Impact
Cotton cultivation and production have a significant environmental impact. This includes water usage, pesticide use, and the energy consumed during manufacturing. It’s important for consumers to be aware of these impacts and to consider them when making purchasing decisions.
Many manufacturers are adopting sustainable practices to reduce their environmental footprint. This can include using organic cotton, reducing water usage, and using natural dyes. Some companies also offer recycling programs for their products.
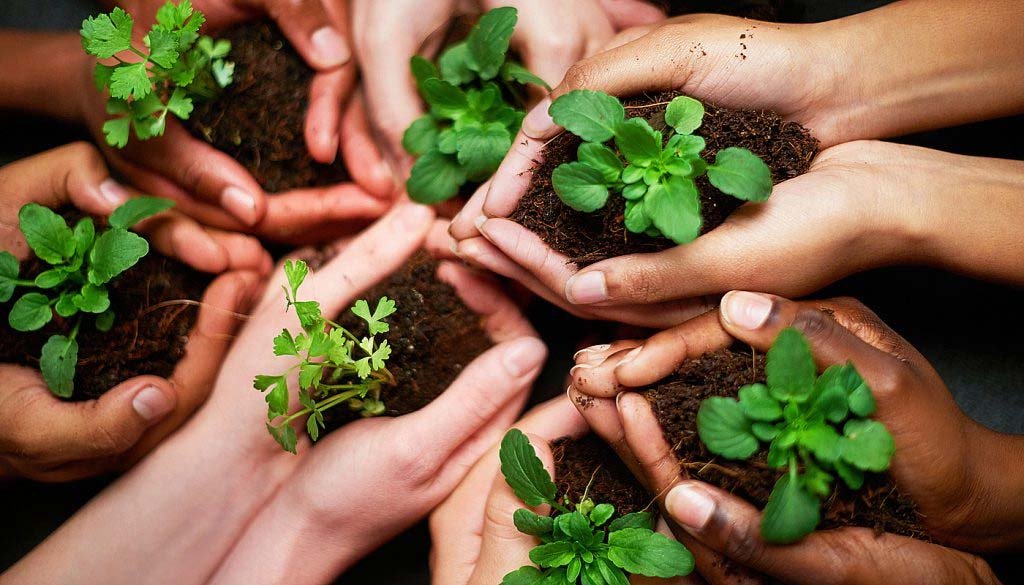
As a consumer, you can make eco-friendly choices by choosing organic cotton products, supporting companies with sustainable practices, and recycling your old textiles. By doing so, you can enjoy the comfort of cotton while also doing your part to protect the environment.
From the planting of the cotton seed to the finishing touches on the bedsheet, each step in the process is a testament to the marvel of textile production. It’s a journey that spans months and involves numerous stages, each with its own challenges and rewards. So, the next time you slip into your cotton bedsheet, take a moment to appreciate the journey it’s taken to reach you. From seed to sleep, it’s a journey worth celebrating.
- Utsav – Festive Print King Size Bedsheet With 2 Pillow Covers – (108*108 Inches, 9ftx9ft)₹1,649.00
- Utsav – Festive Print King Size Bedsheet With 2 Pillow Covers – (108*108 Inches, 9ftx9ft)₹1,649.00
- Utsav – Festive Print King Size Bedsheet With 2 Pillow Covers – (108*108 Inches, 9ftx9ft)₹1,649.00
- Utsav – Festive Print King Size Bedsheet With 2 Pillow Covers – (108*108 Inches, 9ftx9ft)₹1,649.00
- Utsav – Festive Print King Size Bedsheet With 2 Pillow Covers – (108*108 Inches, 9ftx9ft)₹1,649.00
- Utsav – Boota Print King Size Bedsheet – 108*108 Inches – Maroon₹1,649.00